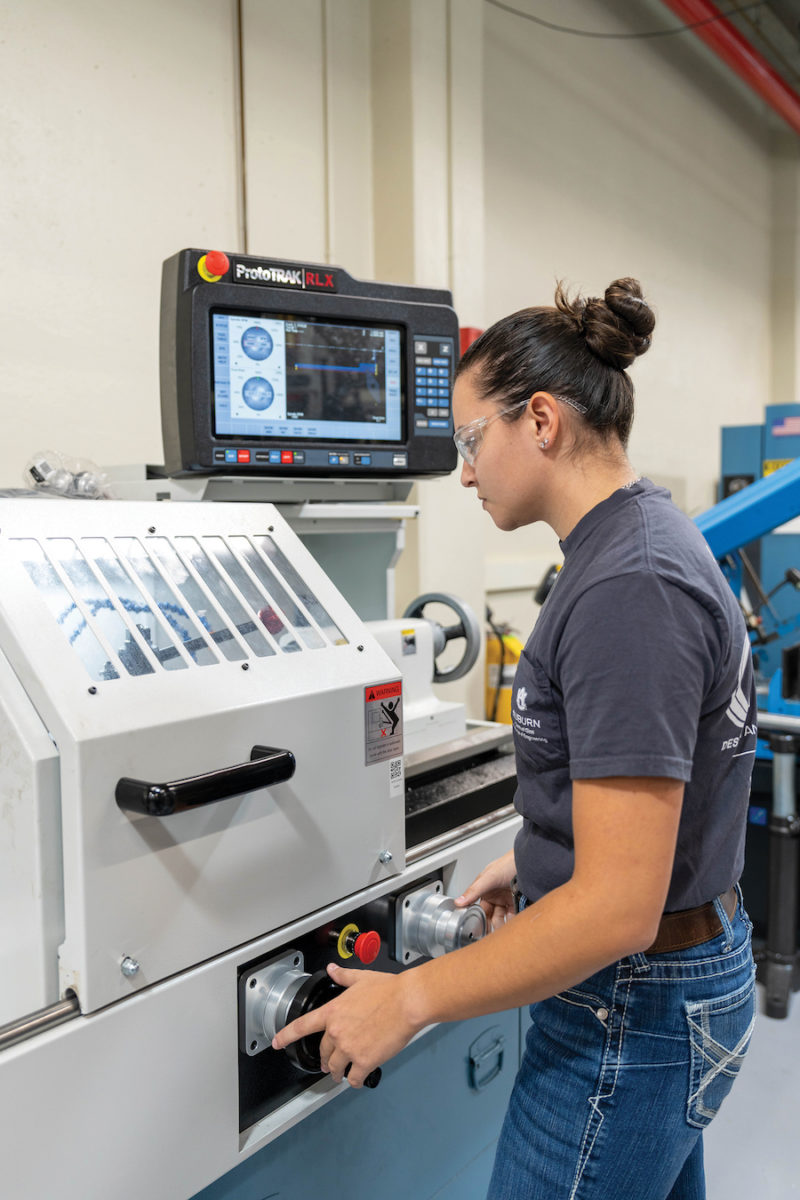
Larry Montgomery believes in education, which trains the minds and hands of young men and women to work skillfully.
If only he’d gone to Auburn.
Montgomery grew up like most future mechanical engineers. In his spare time, he took apart machines and tinkered with engines.
If you needed help fixing your boat, he could lend a hand as best he could.
“But,” he said, “I didn’t know how to do it properly.”
Heading to college, Montgomery assumed, would surely change that. It didn’t.
“When I was accepted for undergraduate study in mechanical engineering, I highly anticipated the opportunity to develop practical skills through hands-on instruction,” said Montgomery, a 1978 Georgia Tech graduate who spent most of his career in engineering and management with American consumer goods giant Kimberly-Clark. “I was disappointed to earn a degree without ever touching a tool.”
At Auburn, he wouldn’t have made it past his third semester without touching one.
They call it — MECH 2020 Manufacturing Technology Lab: “Manufacturing technology lab for introduction of processes such as cutting, forming, machining and joining of metals and other materials. Basic and applied machine shop and manufacturing floor safety.”
The place that makes it possible? The Design and Manufacturing Laboratory (DML) in the basement of Wiggins Hall, home base for the Samuel Ginn College of Engineering’s unique approach to advanced manufacturing education. Which, thanks to the Montgomery Family Foundation — directed by Larry and his wife, Mary — just got a lot more advanced.
“It is a particular passion of ours,” Montgomery said, “to help provide hands-on experiences for undergraduate engineering students.”
Emphasis on “undergraduate.”
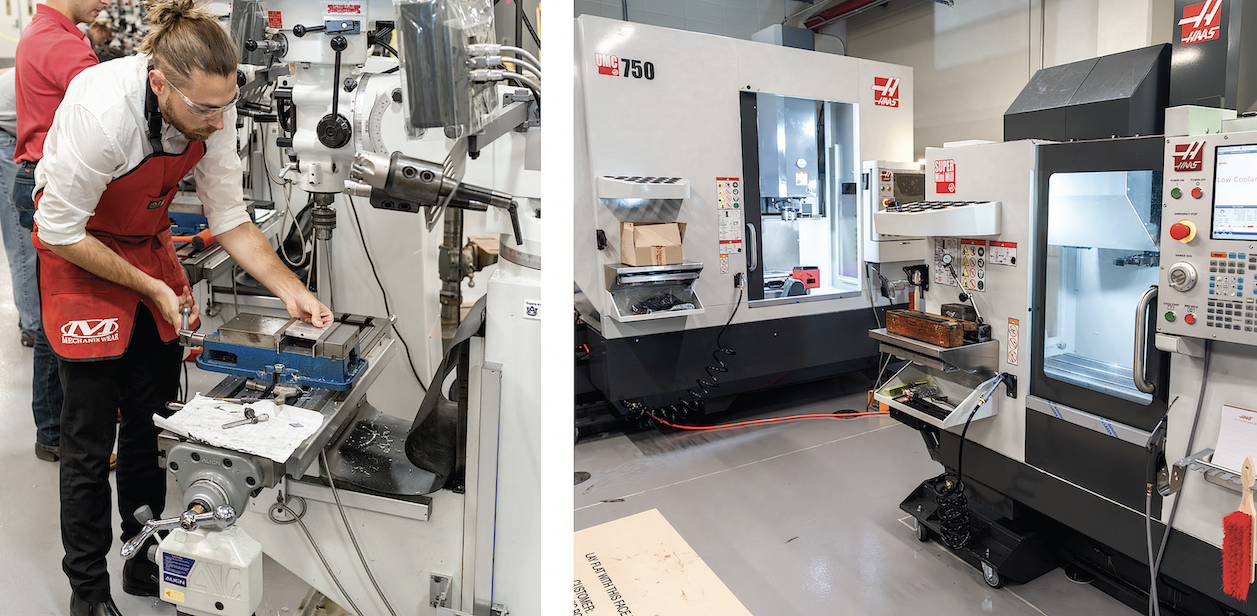
variety of CNC machines — a Haas 5-axis machining center, a Haas 3-axis lathe and two Haas 3-axis machining centers.
“Undergraduate — that’s the key word,” said Jordan Roberts, senior lecturer. “You see similar equipment to what we have in the DML used for research opportunities at several peer institutions, but those are relegated to self-selected upperclassmen for specific projects or research. That’s something we fully support, but Auburn is unique in that, as far as we can see, no other four-year institutions provide their undergraduate students with a hands-on manufacturing experience as full as this one.”
And it’s getting fuller by the month. The DML was born in 2008 in the old Mech Shop, which served the college mostly as a space for research project fabrication.
“Dr. David (Doc) Dyer, who was department chair at the time, decided to convert that shop into what they called the Design and Manufacturing Lab to teach mechanical engineering students how manufacturing impacts design,” Roberts said. “You know there’s that line in the Auburn Creed about this being a ‘practical world.’ Well, Doc was a big believer in that. You can design things all you want, but can you actually manufacture those designs? That’s pretty important. That was the consideration they were trying to impart in mechanical engineering students. That’s what we’re still trying to impart.”
In 2012, the lab moved to the basement of Wiggins Hall. Students came, students went.
The equipment, however, mostly remained the same.
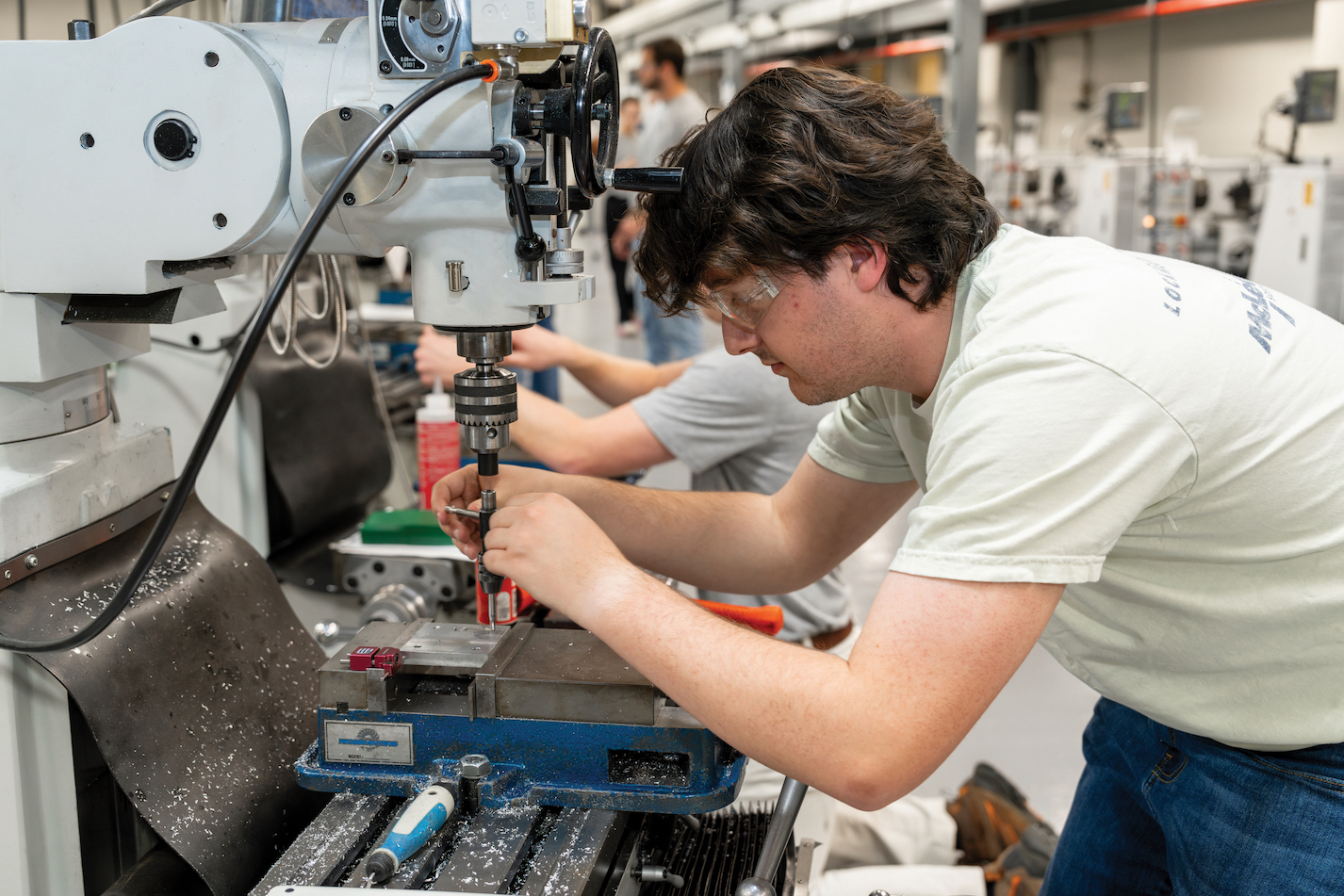
milling machines, lathes (including three manual Bridgeports and two large engine lathes), a Clausing radial drill, grinders and even a powder coat system.
Roberts, who earned a master’s and doctoral degrees in mechanical engineering from Auburn, took the lab’s reins in December 2019. Hopes were high. Then, the world changed.
However, the incredible challenges of the COVID-19 pandemic also brought plenty of unexpected opportunities.
“Not long after I took over, President (Christopher) Roberts, who was then dean of engineering, stopped by the lab for a presentation on safety,” he said. “Afterward, he asked me what could help take the DML to the next level.”
So, in March 2020, as the actual gears ground to a halt, the metaphorical gears started turning.
“When we shut down, we were really able to take stock of what we had, what was working well, what wasn’t working so well and what we could do to really enhance our students’ experience,” Roberts said. “That meant looking not just at the equipment and tools available but how the students were able to engage with them. We talked with college alumni, with alumni of the lab and with friends of the college to come together on how to build on what we had.”
Friends like the Montgomerys.
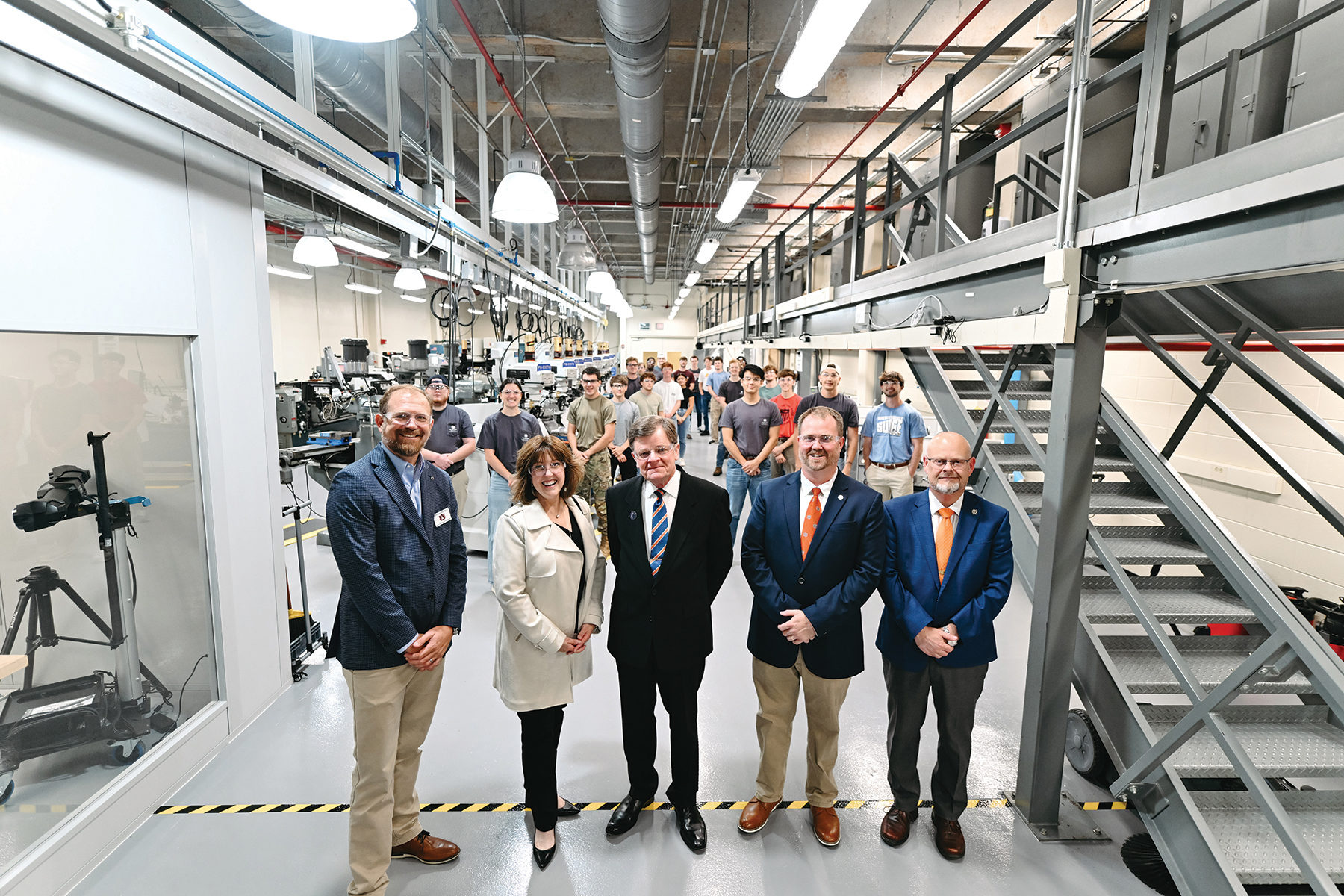
“When we first met with Larry, it was very clear that we both have a passion for undergraduate engineering education that involves hands-on experiences — those high-impact experiences where our students can use the resources in this space to prepare for the career they will have,” Roberts said.
“Thanks to the Montgomery Family Foundation gift, when our graduates walk into those environments, they are now going to be very familiar in ways they havenn’t been in the past,” he added.
Shay Pilcher, a 2021 and 2022 mechanical engineering graduate now working for the Department of Mechanical Engineering as a research engineer, said replicating those enviroments required a few road trips.
“When I took this class several years ago, the machinery and the technology we were using was pretty outdated,” Pilcher said. “It was almost like a hobby-level lab. We were getting experience, but weren’t really being introduced to what was truly out in the industry.
“One day, just after he took over as director, Dr. (Jordan) Roberts found me in class and asked if I wanted to work in the lab and plan how to really elevate what we were offering. What we and some of the other TA’s (teaching assistants) quickly realized is that the lab wasn’t what was represented [to students] when they leave school, which was the whole purpose of that introductory class. So we said, ‘let’s go tour some places, let’s go look and actually ask some questions about what we needed to improve,’ because we really needed to get industry-standard stuff in here,” she added.
They got it in there.
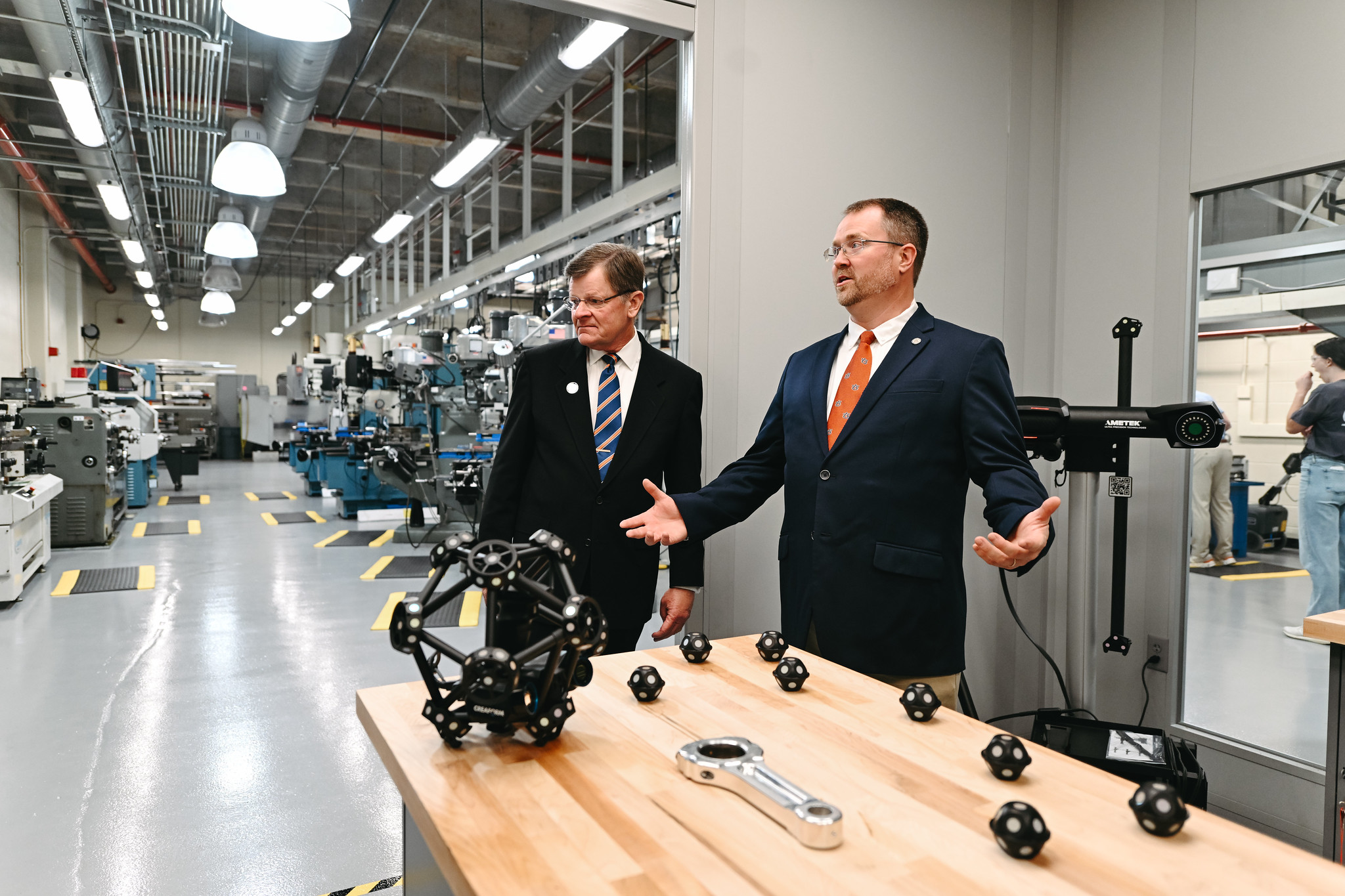
The extensive equipment upgrade built into the $2.75 million renovation of the laboratories and work areas now collectively known as the Montgomery Advanced Manufacturing Laboratories includes a variety of CNC machines — a Haas 5-axis machining center, a Haas 3-axis lathe and two Haas 3-axis machining centers. The lab also features advanced 3D printing capabilities with metal printing systems from Markforged and One-Click Metal, a Stratasys Fortus large-format polymer printer and a Meltio metal printer integrated with the Haas 5-axis machine. In the DML alone, students utilize professional-grade milling machines, lathes (including three manual Bridgeports and two large engine lathes), a Clausing radial drill, grinders and even a powder coat system. The lab also provides dedicated space for student project assembly.
“We now have three different methods of printing metals, which is great given how important additive manufacturing is becoming in today’s manufacturing environment,” he said. “We have an incredible inspection room with half a million dollars in measurement machines, including a state-of-the-art Creaform MetraSCAN 3D scanner that can scan anything from a trinket to a vehicle, which is something we have actually done for some (Department of Defense) partners.”
But the new era doesn’t just include new resources, it includes new offerings. The increased functionality of the space, which now incorporates additional square footage previously utilized mostly for storage, has inspired proposals for seven additional technical electives throughout the next several years supporting a Mechanical Engineering Advanced Manufacturing Certificate.
“Our students can now walk into the DML, and when they go to a co-op, an internship or to their career, they’ll see very similar techniques, very similar machinery and they’ll know the verbiage and the procedures,” Roberts said. “They will be better engineers because of what’s been done here. Again, it comes back to that line in the Creed. We’re instilling the tools for success in a practical world.”
Pilcher agrees.
“Engineers can do things in theory all day long — crunch numbers, make the most beautiful design you’ve ever seen in your life,” she said. “But if you never understand what fabricators and machinists have to go through, if you don’t step into their shoes, you don’t understand the process you have to go through to test those designs and make them real products.
And, in some cases, designs can’t physically be made even with the massive advancements in tech over the past couple of years.
“These classes and these designs are designed to show students, ‘Hey, just because it looks good on paper, doesn’t mean you can physically do it in real life, and if you can’t do it in real life, you have to go back and forth with the machinists and fabricators.’ We’re giving them the knowledge of exactly what they need to be designing. That saves time, that saves money, that makes you a far more effective engineer for a company. And that’s what Auburn is producing — effective and efficient engineers.”
Just like Larry Montgomery wanted to be.
“I came out of college probably as a pretty decent heat transfer and thermodynamics guy, but I was lacking the skills I was really looking for,” Montgomery said at the October dedication of the Montgomery Advanced Manufacturing Laboratories. “Academia of the day determined that it wasn’t relevant, that working with your hands — creating something and holding it in your hands — was passe, that it wasn’t needed.”
“But having spent my career as a mechanical engineer, I am convinced of the value of hands-on experiences to complement classroom instruction. We were motivated to make our gifts because of how the Auburn Engineering culture stresses the practical application of knowledge. This is particularly important for success in business today,” he added.
George Petrie couldn’t have said it better himself.
Meet the Montgomerys
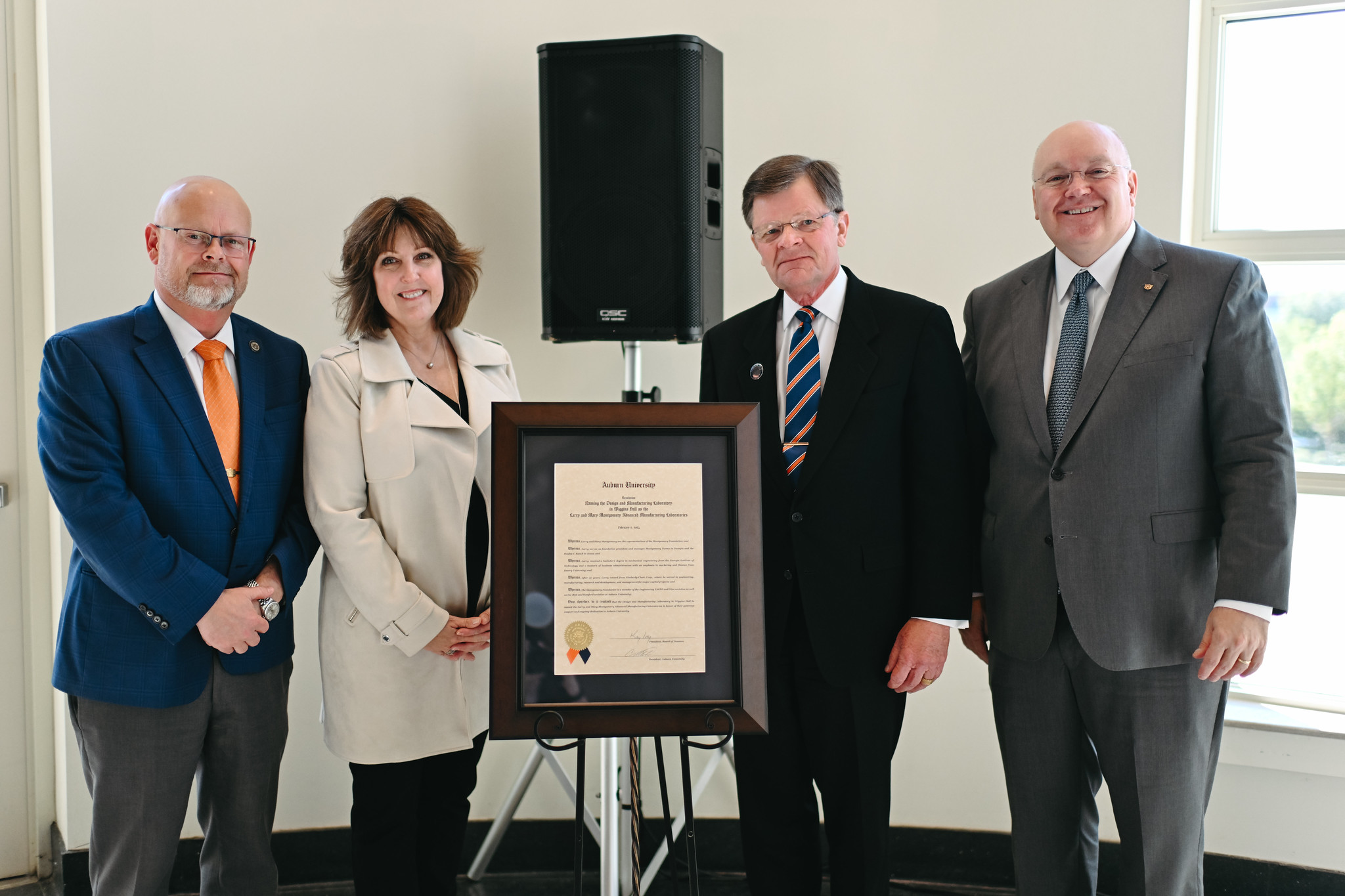
Larry Montgomery earned a degree in mechanical engineering from Georgia Tech and an MBA from Emory University. His career was spent with the Kimberly-Clark Corp. serving in engineering, manufacturing, research and development and management of major capital projects.
Larry’s wife, Mary, earned a degree in business and an MBA from the University of Wisconsin. Currently, she works in the Office of Development at the Georgia Tech. Her experience includes corporate logistics, manufacturing and e-commerce.
Larry and Mary are principals of the Montgomery Family Foundation. The Foundation’s mission is to improve lives through transformational educational opportunities.
The Montgomerys are members of the Engineering EAGLE and Ginn societies as well as the university’s 1856 and Foy societies. They previously supported the Larry and Mary Montgomery Design Studio and the Larry and Mary Montgomery Machine Shop in the Brown-Kopel Center.
A generous investment from the Montgomery Family Foundation made the renovation of the advanced manufacturing laboratories in Wiggins Hall possible. The spaces have been named the Montgomery Advanced Manufacturing Laboratories in honor of their commitment to Auburn Engineering.