Throw out the old rules of manufacturing. Additive manufacturing – more commonly known as 3-D printing – is changing the game, thanks in part to the Auburn Engineering researchers making it happen.
Although 3-D printing has been around for decades, technological advancements have led to new interest in this technology throughout the industry. Manufacturers now have the potential to 3-D print complex components on site, thus shrinking the supply chain, eliminating waste and maximizing profits.
But there remain important questions to answer: Does 3-D printing make sense in all manufacturing scenarios? How do smaller companies take advantage of this technology? Are these components reliable enough to use in critical machinery, such as in airplanes and cars?
Faculty in the Samuel Ginn College of Engineering are addressing these questions through their research in this field. With a growing cadre of faculty members working in additive manufacturing, Auburn is at the forefront of this emerging field of research and is well positioned to assist manufacturers as the industry continues to evolve.
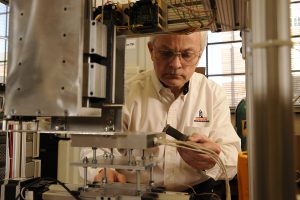
Auburn established the Center for Industrialized Additive Manufacturing in 2016 and appointed Tony Overfelt, William and Elizabeth Reed professor of materials engineering, as its first director. In addition, the college strategically hired two internationally known researchers in the area of additive manufacturing, Nima Shamsaei and Scott Thompson, as associate professors of mechanical engineering.
The process of additive manufacturing involves fabricating components by joining materials such as plastics or metals layer-by-layer from a sliced 3-D computer-aided design model. A laser or an electron beam is used to heat powder, wire or other materials during the fabrication process. This differs from traditional subtractive manufacturing processes, which create products by cutting away materials from a slab.
For industrial use, additive manufacturing provides maximal benefit when producing high-value components with complex or unique shapes that are unobtainable or infeasible to achieve using traditional subtractive manufacturing methods.
“For years, we’ve told engineers, ‘How do you design for manufacturing? How do you design for assembly? How do you design under the constraints of traditional manufacturing processes?’” Overfelt said. “With additive manufacturing, many of those constraints have been removed. Of course, additive manufacturing introduces some new constraints and issues, so it requires a shift in thinking that engineers have to go through.”
Auburn Engineering researchers say additive manufacturing offers unique possibilities that were previously unthinkable. If a part breaks on the International Space Station, there would be no need to wait for a replacement from Earth – astronauts could print a replacement component on site. In the operating room, surgeons could print medical implants during surgery rather than waiting for them to be shipped from across the country. Not all scenarios are right for additive manufacturing, but it opens the door for new opportunities.
Look no further than the GE Aviation plant conveniently located in Auburn to see the potential impact of this technology. In 2015, GE Aviation became an industry leader in this area by launching production of fuel nozzles for jet engines using additive technology in its Auburn facility.
Ensuring integrity of parts
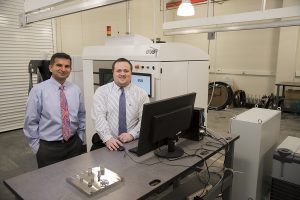
Deep in the heart of Wiggins Hall, Shamsaei and Thompson, co-directors of the Laboratory for Fatigue and Additive Manufacturing Excellence, oversee a facility humming with activity.
The lab’s EOS M 290 direct metal laser sintering system steadily rolls out metal powder on a flat surface inside the machine and then uses a laser to fabricate each layer of an hourglass-shaped piece of titanium.
On first touch, the part feels just as solid as any other piece of metal. But how do we know for sure?
That’s where the other aspect of the FAME lab’s work comes into play. Shamsaei specializes in mechanical fatigue and failure analysis. After fabricating components on the 3-D printer, the laboratory staff can evaluate the integrity of these components on various fatigue-testing machines. Both Shamsaei and Thompson are adamant in expressing the importance of characterizing, understanding and designing for the structural integrity of additively manufactured components.
“It is essential to understand and improve the fatigue and mechanical performance of additive products. In doing so, we can overcome a major barrier against the widespread adoption of this technology,” Shamsaei said. “In terms of durability and reliability of these products, do we trust them enough to put them in an airplane or in a human body? Can they be reliable for their intended applications? That’s what the focus of our research is on.”
The lab’s expertise in both additive manufacturing, as well as fatigue characterization, has proven to be a major attraction to funding agencies and industry partners. Shamsaei and Thompson have led, and continue to lead, additive manufacturing projects sponsored by the U.S. Army, Navy, NASA and private industry, totaling more than $2 million in extramural research expenditures during the past two years. They were also recently awarded $300,000 in funding from the National Science Foundation to investigate their project, “Additive Manufacturing of Fatigue Resistant Materials.”
“Printing a metallic, table-topper sculpture is easy, but consistently manufacturing defect-free, load-bearing parts certifiable for biomedical and aerospace industries is a different story,” Thompson said. “Even one defect in a printed metallic part can prove catastrophic during application. In the FAME lab, we are discovering new ways to predict defect formation and determining how process parameters impact final structural properties.”
Reliable, low-cost solutions
Across the engineering campus in Wilmore Laboratories, Overfelt and his fellow materials engineering colleagues are engaged in unique additive manufacturing research of their own.
In 2016, Overfelt was awarded a $1.5 million grant from the National Institute of Standards and Technology to develop industrialized additive manufacturing technologies for small manufacturers. Unlike the juggernauts of additive manufacturing, such as GE Aviation, smaller manufacturers often don’t have the resources or expertise to incorporate additive manufacturing into their processes.
To help these small manufacturers, Overfelt is experimenting with different input materials and making modifications directly to the additive systems. These projects have the potential to help those working in industry, while also contributing to workforce development as engineering students are gaining early experience with this technology.
“In our labs, we work on the equipment itself rather than using commercial systems with pre-set parameters,” Overfelt said. “We’re actually building the systems ourselves. We think that for the undergraduate engineers here at Auburn getting hands-on experience in building systems, operating systems and developing the process parameters is essential for them to really understand the manufacturing process.”
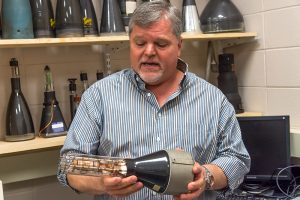
One of the interesting, low-cost additive manufacturing techniques being developed at Auburn is by Bart Prorok, professor of materials engineering. Using salvaged cathode ray tubes from television box sets, he is able to use an electron beam to 3-D print metal components.
“One advantage to not using commercial systems is that it allows us to experiment with different equipment and take more of a research approach to the process,” Prorok said.
Going forward
As the field of additive manufacturing continues to grow and evolve, Auburn is uniquely qualified to help shape this body of research and assist industry in addressing challenges related to additive manufacturing.
“Industrializing additive manufacturing is one of the strategic initiatives of the College of Engineering,” said Christopher B. Roberts, dean of engineering. “The college has a strong commitment to advancing additive manufacturing technology by hiring new faculty and by investing heavily in laboratories and equipment. We see tremendous opportunities to help promote economic growth right here in our region through the deployment of additive manufacturing in aerospace and related high-tech industries.”
The newly renovated Gavin Engineering Research Laboratory opens later this year and will include dedicated space for the university’s additive manufacturing research, including upgraded and expanded test beds. Auburn has also purchased equipment on par with that used at industry-leading GE Aviation.
With the growing number of Auburn faculty working in this area, undergraduate and graduate students have increasing opportunities to gain experience with additive manufacturing technologies through their work in and outside the classroom, which contributes to workforce development in this field.
Moving forward, there will be unique challenges in additive manufacturing that Auburn researchers hope to address. As manufacturing processes become more reliant on internet connectivity, this opens opportunities for cyberattacks against manufacturers who use additive technology.
In future research, Overfelt and his colleagues hope to collaborate with Auburn’s McCrary Institute for Critical Infrastructure Protection and Cyber Systems to address these cyber challenges. Meanwhile, Shamsaei and Thompson hope to continually expand the FAME lab and are teaming up with faculty from the Department of Industrial and Systems Engineering to address unique methods for minimizing defects in additive parts to increase their structural integrity.
As the old rules of manufacturing are thrown out, Auburn Engineering faculty are here to help write the new book on additive manufacturing.