KATELYN RHEINLANDER ’13
Biosystems Engineering
Warehouse Performance Manager for PepsiCo Frito-Lay
SO WHAT DO YOU DO?
I work for PepsiCo Frito-Lay as a warehouse performance manager. I work in a manufacturing facility in Warner Robbins, Georgia. It’s over a million square feet, so it’s the largest Frito-Lay facility under one roof in North America. We have 15 production lines and it’s a full-mix warehouse, and we have our own traffic fleet. There’s a lot going on, and it’s a cool place to work. I make chips for a living.
WHAT KIND OF CHIPS?
All of them. When I first started, Sun Chips and Tostitos Scoops were the two production lines I was responsible for, and there were about 15 people on each. But I got to be part of a start-up, and we put in a brand new fried Cheetos and Smartfood popcorn line. So that’s now four lines and about 35 people I supervise. And that’s just in one department. We have four different departments. If Frito-Lay makes them, we probably make them in that plant. I always say that Funyuns are the coolest to watch cook, because the way the process works is it’s all about air pressure and that’s how they get that puffed up look, and there’s just nothing better than a warm Funyun.
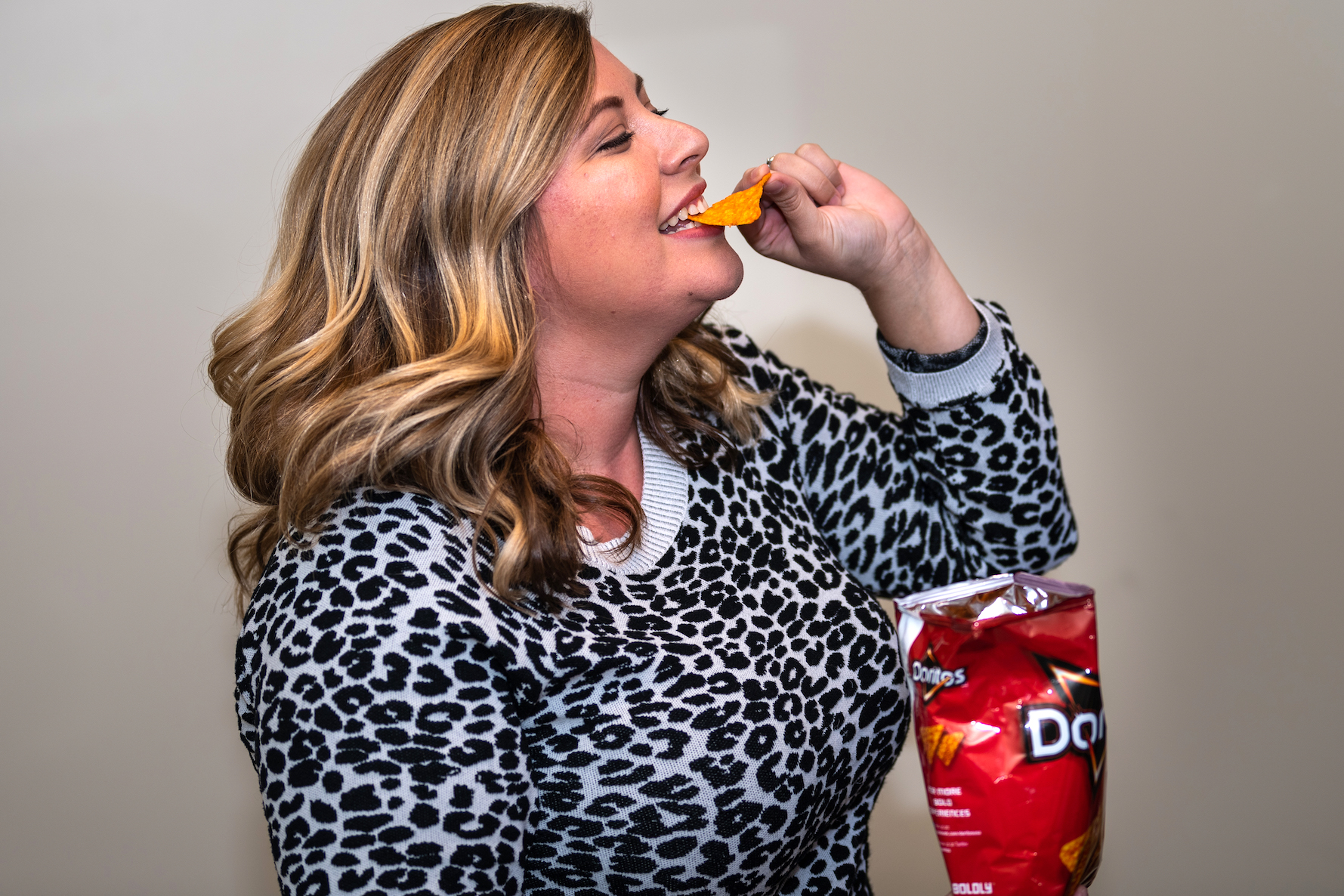
WHY DOES FRITO-LAY NEED ENGINEERS TO HELP MAKE CHIPS?
We hire engineers because we love the way they think. We want people who can problem-solve and troubleshoot. I started in production overseeing packaging, with a team of folks that I managed, and I was in charge of day-to-day operations. It’s really engineering for people — in my eight-hour shift or my 12-hour shift, what problems am I solving for them today? From there, I took over an automated multi-pack line in our carton division, and then recently I transitioned into a role in our direct-to-store model, which is basically how we fill customized orders. So if you want a bag of Lays, a bag of Doritos, and a bag of Smartfood, we’re going to take those individual orders and send them off to gas stations and grocery stores. I’ve gotten to do a lot of different things all in one facility, and it’s just a neat environment. It’s a lot of young managers, so there’s like 30 or 40 of us under the age of 30. It’s just a really fun group to get to be with. There’s 10 or 12 of us from Auburn.
HOW HAS YOUR DEGREE SERVED YOUR CAREER?
If you had asked me, coming into biosystems, if I had wanted to make chips for the rest of my life, I probably would have laughed at you. But I think the thing that biosystems has given me is the confidence to go do whatever I wanted to do. What initially drew me in was the idea of fostering sustainability and working on environmental impact. I felt like, in the world that we function in today, those issues are so critical and important. And I also loved the idea of a little bit smaller department — at least it was smaller when I started — and the ability to get that one-on-one attention with some of the best professors across the board. I describe it as a combination of environmental and agricultural engineering, but I think we talked about it sometimes as a jack-of-all-trades degree. We take classes in electrical, we take classes in coding, in agricultural and environmental and civil. Whatever you decide to go do, you have the tool skillset and the capability to go do that and so I loved the options that it provided me. What I valued the most is that it put me in situations where I didn’t know how I was going to finish something, how I was going to finish this homework assignment, how I was going to finish this project. But it provided me with the support and push to go do it. Every day at work I run into similar situations, and I feel confident that I can go solve that problem because I’ve done it before. I’ve come to a stop in the road and said ‘I don’t know how I’m going to have to do this’ — every time I’ve had homework in heat and mass transfer — and I’ve come out the other side and said, ‘no, I can do this,’ and that’s given me the confidence to go make chips.