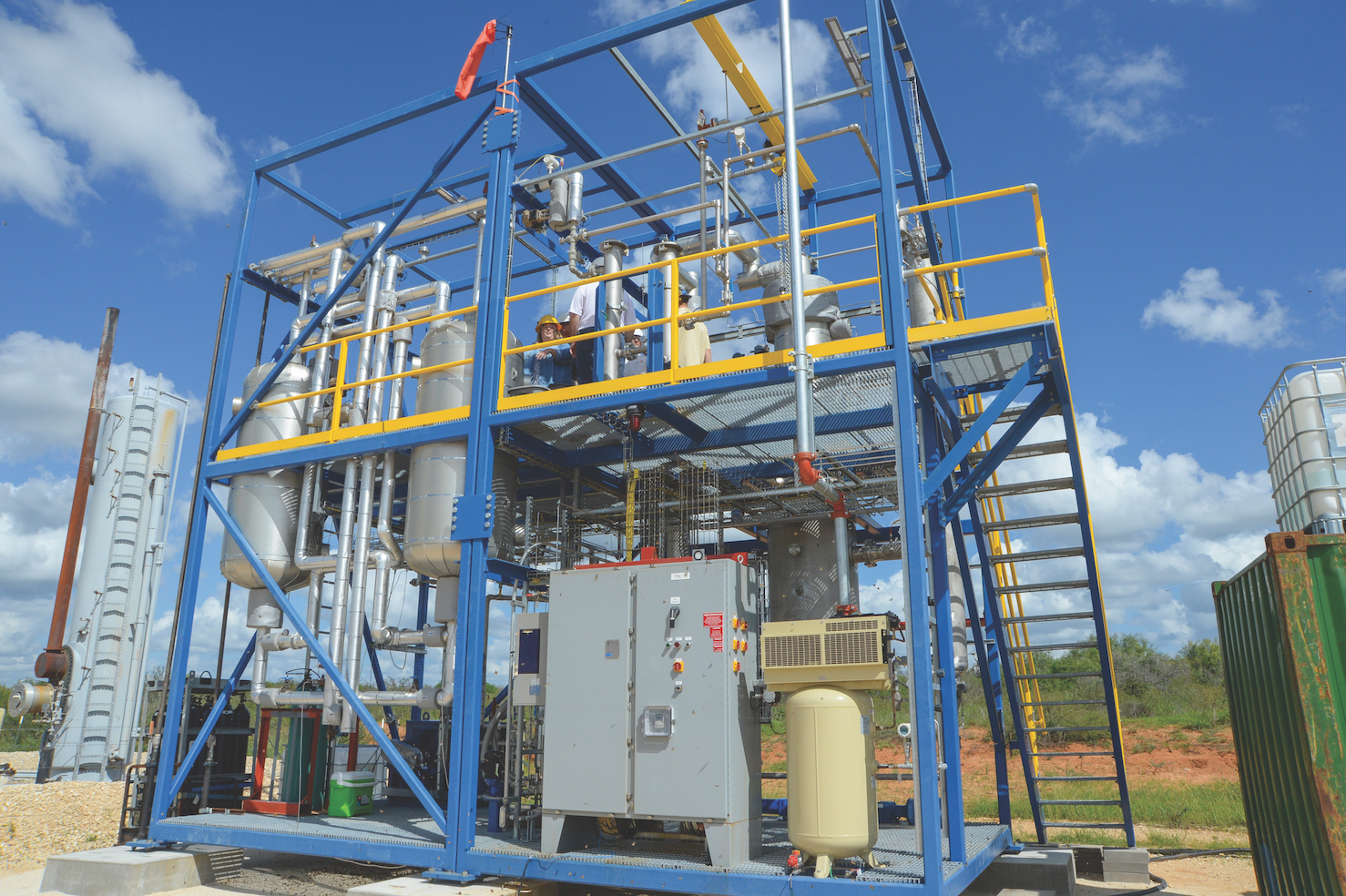
Bruce Tatarchuk, who has long been recognized for his work in catalysis and microfiber technologies, is taking a new direction in his research that looks to bold frontiers in energy. His latest effort is literally taking place at the end of a long road – in the scrublands of Texas where oil and gas fields reign supreme.
It’s where Tatarchuk and his team are running a pilot project that aims to reclaim natural gas that would otherwise go unused because it is ‘sour’ in the vernacular of the industry. Too high in sulfur content, it is either flared, vented or capped at the well, a shutting-in process that generally costs more than $500,000 per well after $2 million is spent drilling it.
“The presence of hydrogen sulfide or mercaptans (organic sulfur compounds) in natural gas is what causes the problem here,” Tatarchuk explained. “We remove the sulfur in a way that is much more efficient than traditional approaches, by using a patented selective oxidative catalyst that directly transforms 97 percent of sulfur contaminants into elemental sulfur.”
Tatarchuk notes that traditional methods of desulfurization generally cost significantly more than a dollar per thousand cubic feet of natural gas. The approach that his group is developing cleans the gas up for 13-17 cents per thousand cubic feet.
At the heart of the process is a skid-mounted pilot unit that the Auburn team installed about an hour from San Antonio, Texas, in the Eagle Ford Shale gas and oil field. Called the Sourcat 100 MSCFD System, it was demonstrated for a 540-hour run that culminated in October. Its oxidative sulfur removal process converted up to 97 percent of the hydrogen sulfide in the gas stream into elemental sulfur.
“This process resulted in the production of pipeline-spec natural gas,” Tatarchuk said. “We pulled in gas with sulfur concentrations ranging from 125 ppm (parts per million) to 2,000 ppm and successfully treated it to an outlet gas sulfur level of less than 4 ppm. It works even when the level of sulfur in the gas varied widely, which is often not the case with other technologies.”
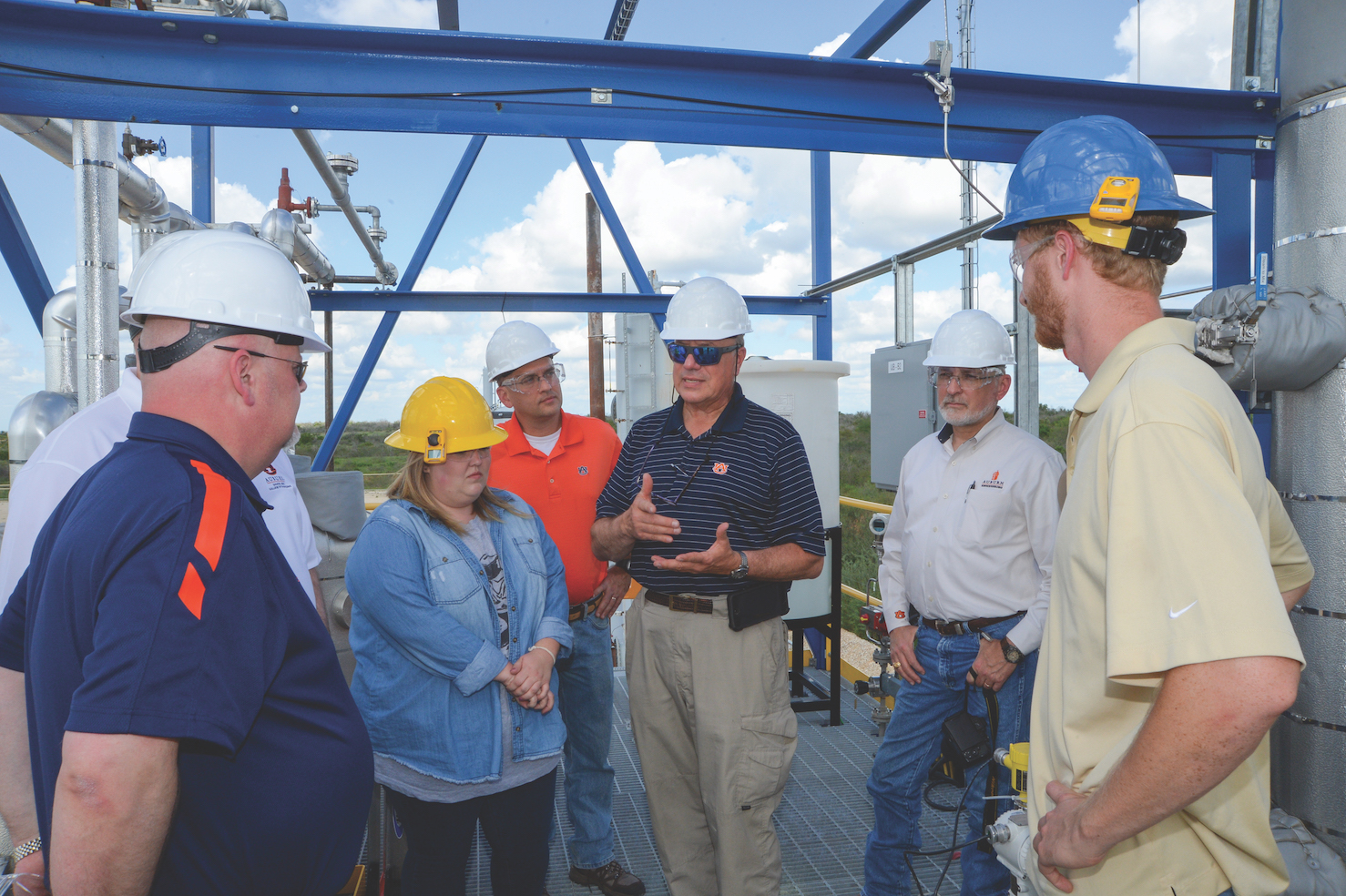
Tatarchuk, who is widely recognized for his career-long work in catalysis, also noted that the catalyst used in the process is cost-effective, and robust, showing no signs of deactivation when it experiences feeds with high levels of condensable hydrocarbons.
“We also gave it real-world testing involving multiple shutdowns that are caused by external events,” Tatarchuk added. “These kinds of stop-and-go cold starts are a true test of the efficacy of the system, and even under these conditions we experienced up to 97 percent removal of H2S (hydrogen sulfide).
Tatarchuk points as well to the flexibility of the system, which can be placed at gathering points, compressor stations, sales points and even directly at the well head. It also offers remote monitoring capabilities and emergency shutdowns with alarm notifications.
“We have two to three Auburn engineers on site at the pilot plant that is staffed 24/7, but I always like to point out that what they are monitoring can be done off-site as well, and will be in the future,” Tatarchuk said. “I always like to say that one of our co-op students can literally monitor the process from his dorm room.”
The pilot site is essentially a tenth-scale rendition that has proven the success of the process.
“When we scale this to a commercial level we will be able to produce gas at a far lower cost, and in smaller volumes, than competing processes, so it means that shut-in, flared, vented or unproduced gas can be brought to market,” Tatarchuk explained. “This represents as much as 30 percent of the gas associated with the Eagle Ford and Bakken formations.”
To put it in perspective, he noted that a city the size of the Washington, D.C., metro area could “run off of that amount of gas ten times over.”
In addition to the jobs and energy security that would be a part of the economic potential, Tatarchuk points to environmental benefits as well.
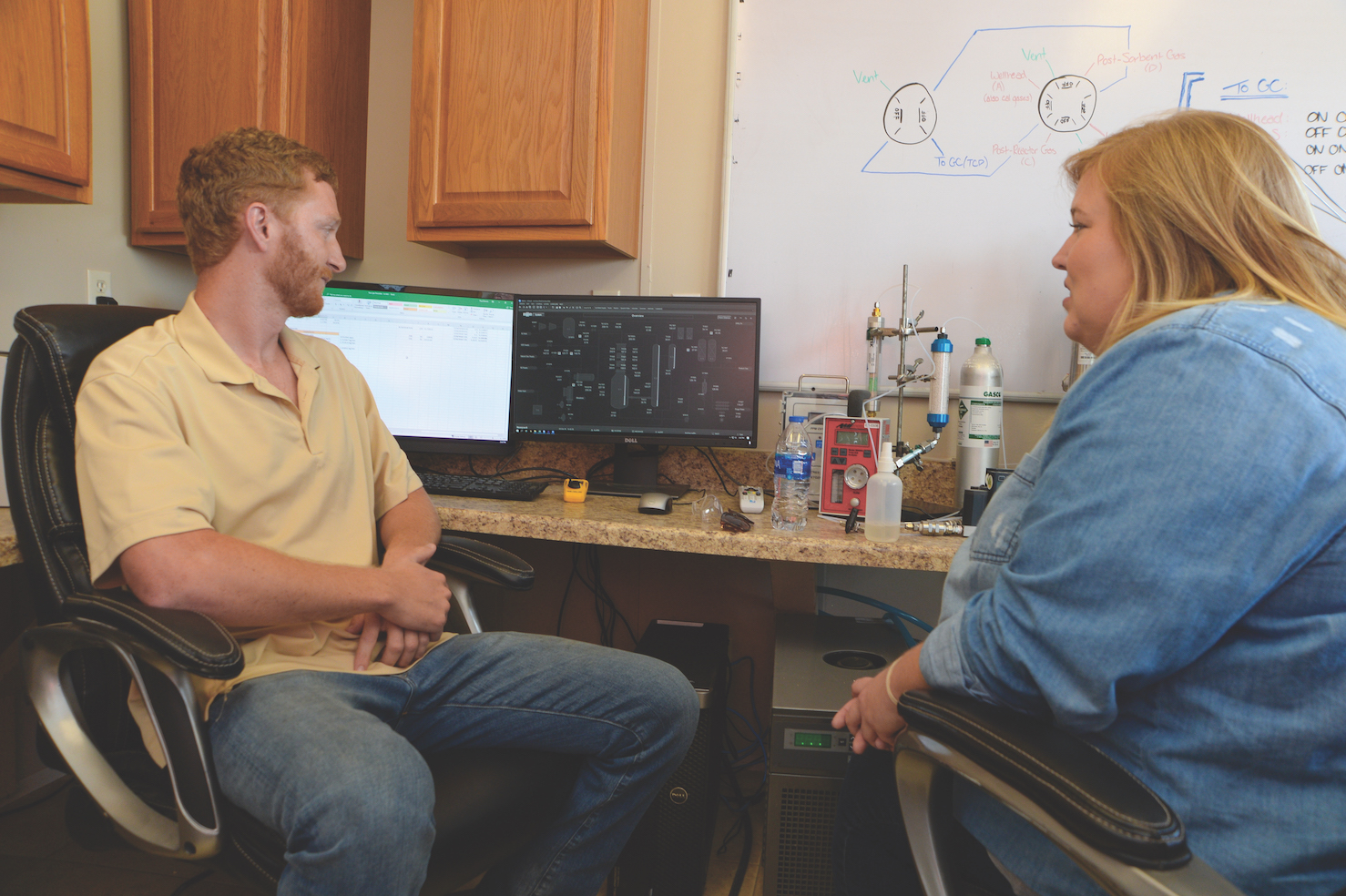
In terms of global warming, vented methane absorbs infrared radiation at night 20 times more strongly than CO2, he points out. But the primary benefits will be economic in nature, with new electric generation capacity generally moving to gas from coal and nuclear.
“The challenge in this scenario is cleaning up ‘sour’ gas to the point that it can be produced and moved,” Tatarchuk said. “And to do so economically, which is where we come in. We are looking beyond the current technology of $25 million scrubbers, and we are not using large-scale plants and chemical scavengers with our process. We can make pipeline-spec gas in a single pass, using a robust catalyst.” He adds that the Sourcat system is modular and more easily moved from site to site as wells move through their production cycles.
“It means better access to what the industry calls stranded or remote wells, because their output level doesn’t justify building pipelines that can handle the corrosive nature of gas with either low or high sulfur content. I like to call them ‘hindered’ wells, however, because there is a fix to this situation that our technology addresses.”
Finally, Tatarchuk noted, that in addition to economic and environmental factors, this new process would bring added stability to the natural gas grid, which is only a step away from the electric grid.
“Unlike liquid fuels, natural gas cannot be stored, so this technology provides a new technology that can assist the energy grid through a higher level of efficiency at a lower cost,” he concludes. “It’s a win-win situation for all involved.”